DataLyzer
O que é FMEA?
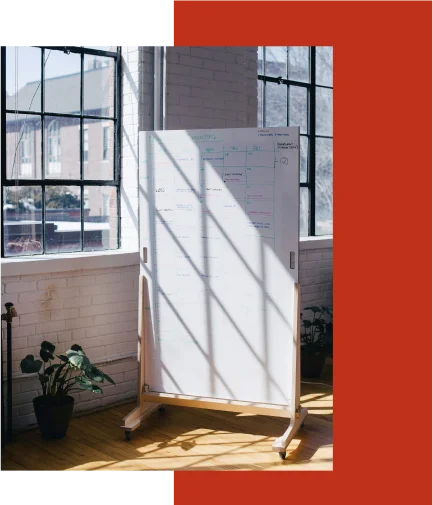
O que é FMEA?
Atualmente, a Análise dos Modos de Falha e seus Efeitos (FMEA) é a técnica mais utilizada na análise de riscos. A análise de risco é uma atividade humana muito natural. Imagine-se como um caçador-coletor encarregado de organizar a refeição da noite. Juntamente com sua equipe, você organiza uma festa de caça e parte desse plano fará uma análise intuitiva dos riscos. Quais são os perigos? Você pode considerar predadores, sede e lesões durante a perseguição. Todas as precauções que você toma resultam em uma caçada bem-sucedida, todo mundo volta para casa inteiro e a tribo come o jantar.
A análise de risco continua sendo uma parte essencial de nossa atividade comercial. Analisamos rotineiramente situações e tomamos ações para minimizar os riscos comerciais e as preocupações com segurança. O FMEA é um método eficaz de análise de risco para projeto e fabricação.
Ele examina os processos de design e fabricação e identifica as oportunidades de marginalidades e defeitos que podem resultar em insatisfação do cliente.
Antes de entrarmos em detalhes, por que não realizar um teste simples. Desça sua linha de produção e pense consigo mesmo: “O que pode acontecer com o produto aqui que afetará o cliente? O que estamos fazendo sobre isso?” Pergunte à equipe de produção o que costuma dar errado no processo e pense em “Como isso pode afetar o produto”. O FMEA capturará todo esse conhecimento e experiência de maneira estruturada e permitirá que você execute ações que minimizem o risco de um cliente decepcionado.
Uma breve história do FMEA
O FMEA foi desenvolvido pelos militares americanos no final dos anos 40. Entendo que suas frustrações com o mau funcionamento das munições os levaram a desenvolver uma metodologia que eliminaria todas as possíveis causas-raiz. Um método detalhado foi documentado: MIL-P-1629.
Funcionou e foi adotado pela indústria aeroespacial e nuclear. A NASA creditou o sucesso dos pousos na Lua por seu uso. A NASA também estava preocupada com alimentos contaminados em missões espaciais, pois eles desenvolveram uma técnica muito semelhante chamada HACCP (Análise de Perigos e Pontos Críticos de Controle) especificamente para a indústria de alimentos.
Nos anos 70, os desvios de baixa velocidade envolvendo o Ford Pinto resultavam em incêndios fatais se o tanque de gasolina se partisse. Como você pode imaginar, foi um desastre de relações públicas. Para eliminar a reincidência deste e de outros problemas sérios, a Ford Motor Company implementou o FMEA em seu processo de design.
Mais organizações usavam o FMEA como ferramenta de análise de risco e, em 1993, o AIAG (Automotive Industry Action) Group) incorporou-o ao padrão QS9000 para produção automotiva e seus fornecedores. O QS9000 tornou-se TS16949 e, desde novembro de 2016, IATF16949.
Embora o FMEA visasse especificamente o setor automotivo, outras indústrias que exigem os mais altos níveis de confiabilidade, por exemplo, semicondutores e petróleo e gás, o implementaram. Esses padrões de confiabilidade agora estão se estendendo a produtos de linha branca e produtos eletrônicos do dia a dia. Estritamente o formato atual é FMECA (Modos de falha e efeitos e análise de criticidade), a Criticidade do defeito para o usuário final é incorporada ao método.
Para fins práticos, é uma análise de risco e redução de defeitos. técnica que leva em conta três coisas; a severidade do defeito para o usuário final, a ocorrência da possível causa raiz e nossa detecção eficaz ou eliminação desta causa raiz.

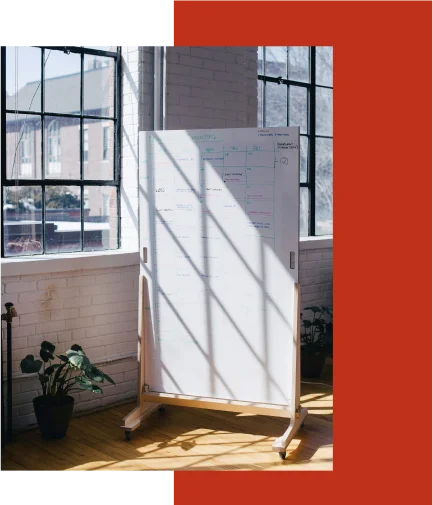
Introdução à análise de risco
Uma parte importante de qualquer análise de risco é o escopo do processo. Isso pode parecer trivial, mas é essencial saber se sua análise deve incluir, por exemplo, a loja de materiais recebidos. Então precisamos fazer um fluxo completo do processo. Essa é uma tarefa crucial e deve incluir todas as etapas do processo, incluindo as de retrabalho. Em cada uma das etapas do processo, precisamos identificar as possíveis fontes de variação e possíveis problemas. Precisamos documentar os defeitos que podem ocorrer no produto.
Também precisamos listar os problemas de equipamentos e processos que podem causar defeitos no produto. Em um processo de análise de risco, a criação de um fluxo completo do processo e uma lista completa de possíveis problemas podem levar 50% do seu tempo.
De onde vêm as idéias?
Tradicionalmente, uma técnica de brainstorming tem sido usada para gerar uma lista de possíveis problemas em cada etapa do processo ou etapa do projeto. Embora isso seja útil, geralmente é mais útil incorporar todas as suas fontes de variação atuais em seu FMEA inicial. Estes incluem:
– Entradas de incidentes de sucata
– Entradas de devoluções de clientes
– Entradas de quase acidentes
– Entradas do próximo processo
– Ideias dos designers
– Ideias dos operadores de máquinas
– Ideias da equipe de manutenção
– Se você tem CEP, considere pontos fora de controle
– Incidentes em equipamentos similares
– Conselho de especialistas do setor
– Assessoria de seus fornecedores de materiais e equipamentos
O uso dessas fontes capturará muitos problemas e marginalidades que já existem e tornará seu FMEA prático e útil desde o primeiro dia.
O layout do FMEA da IATF16949
Ao avaliar riscos potenciais em um processo, é útil documentar as informações em um formato FMEA estruturado. O formato IATF16949 da Indústria automotiva é amplamente utilizado e um exemplo é mostrado no gráfico a seguir;
Nas 4 primeiras colunas, você documenta as etapas do processo, os requisitos do processo, os modos de falha em potencial e os efeitos das falhas. Na próxima etapa, você identifica os problemas do processo que podem causar a falha e os controles existentes para prevenir ou detectar os problemas. As colunas finais contêm as ações corretivas tomadas e os resultados dessas ações.
A Gravidade, Ocorrência e Detecção são todas dimensionadas de 1 a 10. 1 é a melhor classificação e 10 é o pior. Multiplicá-los juntos fornece o Número de prioridade de risco (RPN). Originalmente, o FMEA tinha como objetivo diminuir o número de RPN, mas a detecção é menos importante que a gravidade e a ocorrência; portanto, a gravidade e a ocorrência estão ficando mais importantes. Toda esta informação é armazenada no FMEA. Quando um ciclo de aprendizado for concluído, o FMEA será lançado. O FMEA é um documento ativo e será revisado e atualizado regularmente. Novas causas, modos de falha e serão adicionadas à medida que você aprender mais sobre seu processo.
Software FMEA
A maioria das empresas começa a aplicar o FMEA no Excel. Embora o Excel seja realmente flexível, não é realmente adequado aplicar o FMEA. O usuário precisa fazer muito trabalho extra para seguir as regras do FMEA, criar os documentos, criar links entre o fluxo do processo, o FMEA e o Plano de Controle, mas principalmente manter os documentos.
Para começar rapidamente com o FMEA, você pode baixar uma versão de avaliação do nosso
Software FMEA . O DataLyzer FMEA é muito econômico em comparação com a implementação de seu próprio sistema no Excel. A versão de teste pode ser usada por 30 dias; portanto, o mínimo que ele fará é ajudá-lo a iniciar a implementação do FMEA, sem nenhum custo. Esta introdução também está disponível como um white paper. Na página, White Papers , você pode encontrar mais informações sobre o FMEA.
Treinamento on-line e seminários on-line gratuitos
O DataLyzer oferece treinamento de FMEA on-line muito econômico. Para obter mais informações, faça o download do PDF aqui .
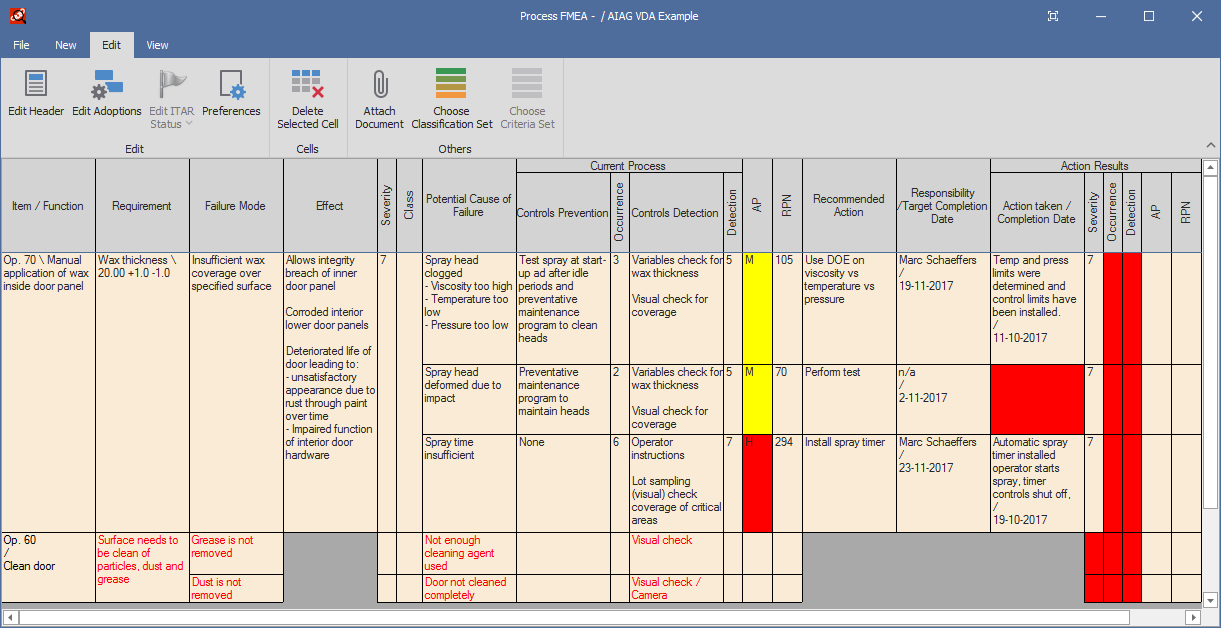